On the Factory Floor: Dr. Martens’ Cobbs Lane
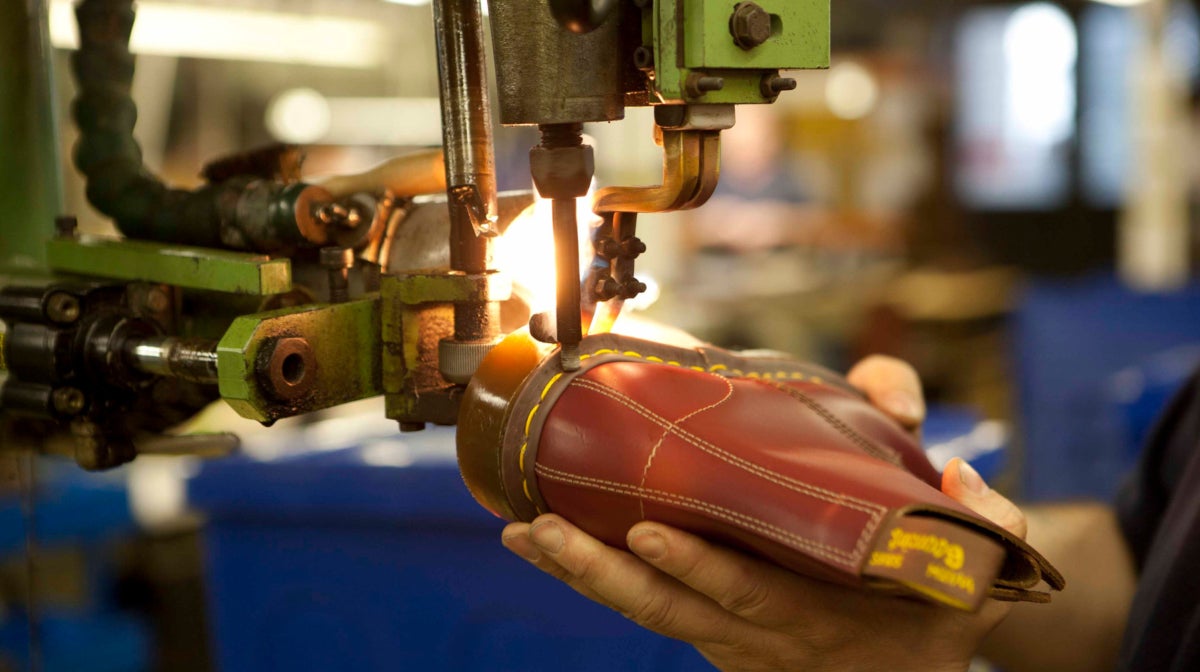
Founded on traditional shoemaking techniques dating back to post-World War II,
A lot has changed since the first pair of Dr. Martens 1460s rolled off the production line in 1960, but one thing that hasn’t changed too much is the brand’s iconic UK Cobbs Lane factory. Dr. Martens has made shoes in the factory since 1960 and continues to do so until this day. The meteoric rise of the brand meant that the factory simply couldn’t keep up with demand, so today it is predominantly the
Dr. Martens invited us to take a look around the Cobbs Lane factory, the birthplace of some of British shoemaking’s most iconic silhouettes. Entering the factory floor, we are greeted with the smell of freshly cut leather and an orchestra of machines all being worked to create the latest batch of shoes. On one side of the factory, rolls of soft leather sit waiting to make their way through the assembly line, while at the other end highly-skilled machinists mold the upper and sole with a heated blade at 700°C before they are neatly wrapped up in a premium red Made in England Shoebox. Join us on a visual trip around the Cobbs Lane factory.
The 5-Step Factory Process:
1: CLICKING
The finest sections of leather are cut to create the shoe's uppers. For the standard required for a 'Made in England' product, the Clicker needs experience, a steady hand and, above all, an eye for detail.
https://www.youtube.com/watch?v=yfJrQh3DeeE
2: CLOSING
The upper panels are sewn together with a tough "Puritan" stitch, three lines of stitches using very heavy weight cord thread for durability.
https://www.youtube.com/watch?v=SL06knHBGS4
3: WELTING
The PVC Goodyear welt is skillfully stitched by a machinist on to the upper, using our instantly recognisable yellow thread.
https://www.youtube.com/watch?v=G3682-FcQDo
4: FUSION
Using a blade heated to 700 degrees centigrade, a highly skilled machinist seamlessly fuses the upper and sole of the boot together.
https://www.youtube.com/watch?v=p2tV2qS5Ksk
FINISHING: The finished boot gets a hand-polish and lace-up, before being boxed and shipped to stores.
https://www.youtube.com/watch?v=Ii2Dn7QFJpA
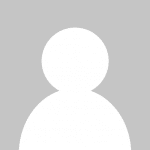